毎日のように身に着けるジュエリーですが、その作り方をご存じの方は意外と少ないのではないでしょうか。 実は完成までには非常に多くの工程があり、それら一つ一つを専門職人の技術が支えています。普段滅多に知ることのできないジュエリー製作のプロセスをご紹介します。「こんなに手間がかかるの?!」と、きっと驚くことでしょう。
大きな流れは…
Ⅰ:デザイン →Ⅱ:原型作り →Ⅲ:ゴム型作り →Ⅳ:ワックス・キャスティング →Ⅴ:仕上げ →完成
ではそれぞれ細かく見ていきましょう。
Ⅰ:デザイン
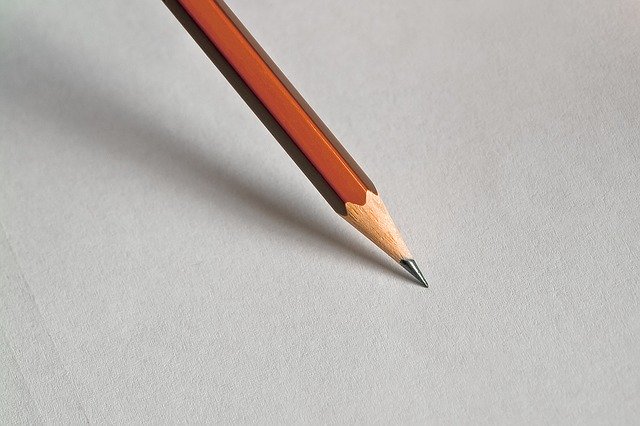
作りたいジュエリーのイメージを画像に起こします。「絵を描くだけでしょ?」と思うなかれ。製造~販売までのあらゆる条件を加味してデザインする…となると、「ただのお絵かき」という訳にはいきません。
※顧客の希望を反映する「オーダーメイド」の場合は、多少プロセスが変わってきます。
①マーケット情報の収集&具体的検討
まず消費者ニーズ・流行・景気等を調査し、作りたい商品の大まかなコンセプトを決めます。そしてどんな素材を使って、いくらで販売するのかなどを具体的に検討します。
②デザイン企画
「付き目」(実際に使う金属の量のこと)・石の留め方・表面処理の方法など、①で決めた詳細を織り込んで、イメージをデザイン画に起こします。手書き・PCなど方法は様々ですが、実際に製作するスタッフに正確な情報が伝わる画像にすることが重要です。三面図(上・正面・側面)と立体図を原寸大で描くことが多いです。
③製作企画
出来上がったデザイン画通りに作れるか、製作スタッフと検討します。特に、完成品のベースモデルとなる「原型」を製作するスタッフには、デザイン上のポイントや加工の注意点などを的確に伝えます。
Ⅱ:原型作り
ジュエリーの金属部分は、「キャスティング(熱で溶かした金属を、型に流して固めること。鋳造ともいう)」という方法で作ります。完成品と同形の空洞を「型」の内部に設け、ここに溶けた金属を流して固めると、同じ形の製品が作れる…という仕組みです。では「完成品と同じ形の空洞」をどうやって作るのか?そのカギとなるのが、「原型」です。
製造過程では「溶かした材料を型に流し込む」という作業が複数回登場します。しかし型の素材を変えたり、使用した型を壊して中身を取り出したりするため、型はその都度新しく用意します。この時に重要なのは、型の内部空洞の形は、どれも毎回ピッタリ同じでなければならないということ。それならば、あらかじめ完成品と同形の「原型」を作製し、毎回これを元に型を作れば、いつもピッタリ同じ形のものが作れるという訳です。
原型の材料には銀(以後SVと表記)を使います。「原型の生き写し=完成品」ですから、デザイン画とデザイナーの意向を忠実に立体化することが求められます。この工程を疎かにすると、完成品の出来が大きく左右されてしまうため、デザイナーと原型スタッフとの間では検討・作り直しが何度も繰り返されます。現在主流となっている「CADによるデータ作成→3Dプリンターによる造形→SVで鋳造」という方法をご紹介します。
①ジュエリーCADによるデータ作成
「ジュエリーCAD」は、ジュエリーの立体的な設計図を作るソフトのこと。実際の寸法等を入力しながら3D化した完成予想図を作ります。データで管理ができるため、原形作りに取りかかる前に何度でも修正が可能です。視覚的効果が絶大なので、デザイナー本人がジュエリーCADを使ってデザインをすれば、よりリアルに自分のイメージを伝えることができます。様々な種類があり、ジュエリーが不得手としてきた有機的なデザインを作れるソフトも登場しています。完成データは、そのまま「3Dプリンターによる造形」で使用します。
②3Dプリンターによる造形
①で作ったデータを3Dプリンターに読み込み、キャスタブルレジンという素材でできた立体物を造形します。質感こそ違えど、デザインや大きさは完成品と同じなので、具体的な検証に大いに役立ちます。アイデアが実際に「形」となったこの造形物を使って、実際の原型製作に入ります。
③ツリーの製作
まずは大まかな流れをご紹介します。②でできた造形物は、高温で熱すると溶ける性質があります。この造形物に、熱すると溶ける素材でできた棒を一本溶接し、熱に強い分厚い素材で隙間なく包みます。この時、棒の端が少し外に出るようにします。この塊を高温で熱するとどうなるか…。周囲を固めた分厚い素材に変化はありませんが、中の造形物と細い棒は溶けてしまいます。外にとび出たせた棒と塊の境目は穴となり、溶けた「造形物+棒」はそこから外に流れ出ます。すると内部には「造形物の形の空洞」と「外に繋がる通路」ができ、この塊全体は「原型を作るための型」となります。SVでキャスティングをすれば、原形が完成…という流れです。
では工程ごとに見ていきましょう。まず、熱すると溶ける素材でできた短い棒を造形物に溶接します。造形物部分は空洞になり、棒の部分は、溶けた造形物や地金の通り道である「湯(ゆ)道(みち)」になります。土台となるゴム製円すい台の中央に、熱すると溶ける素材でできた細い棒を立て、「造形物+棒」を放射状に溶接します。その姿が木に似ているので、「ツリー」と呼びます。
④埋没材流し込み
次に、熱に強い素材でツリーを包みます。③で作ったツリーをステンレス製の筒の中に置き、「埋没材」と呼ばれる液体を流し込みます。液体なので隙間なくツリーを覆うことができ、ツリーは埋没材の中に浸かった状態になります。
⑤脱ろう・焼成
この筒を高温の電気炉で焼きます。筒内部の「造形物+湯道」は溶けて外に流れ出て、内部にツリー型の空洞ができます(=脱ろう)。同時に「埋没材」は熱によって陶磁器のように固くなります(=焼成)。焼成が終わると、この筒自体が「原型用の型」となります。
⑥キャスティング(=鋳造)
原型用素材のSVを高温で溶かし、遠心や加圧などの方法を使って⑤の内部にできた空洞に流し込みます。
⑦冷却・埋没材除去
キャスティングが完了した筒を水に入れて冷やします。すると埋没材部分が壊れ、中から固まったSV製のツリーが現れます。こびりついた埋没材をきれいに取り除き、ツリーから「造形物の形の部分(=吹き上がり)」を切り離します。
⑧原型完成
磨いて形を整えたら、原型の完成です。
Ⅲ:ゴム型作り
最終的な製品製作段階に入っても、実は「原型作り」と同じ手順(ツリー製作→脱ろう・焼成→キャスティング)で作業を進めます。そこでまず必要となるのが、「熱すると溶ける造形物」です。素材には高温で溶けるワックスを使うため、この造形物を「ワックスパターン」と呼びます。原型製作時には3Dプリンターを使いましたが、1つ出力するのに何時間もかかるため、効率が悪いのが難点。そこでⅡ章で作った原型を使い、「『ワックスパターン』を作るための型」を作ります。これがあれば多くのワックスパターンを効率よく作れるため、量産にも対応できます。
①湯道の取り付け
完成した原型には湯道がないので、SVの細い棒を最適な場所に溶接します。
②ゴム型に原型をセット&ホット・プレス
ワックスパターン用の型にはシリコンゴムを使用します。まず①で作った原型の湯道部分に三角すいの金属型を取り付けます(完成したゴム型のワックス注入口を広めに確保するためです)。アルミ製の四角い枠内にやわらかいシリコンゴムを敷きます。そこに湯道と三角すいを取り付けた原型を置き、上からシリコンゴムをかぶせ、アルミ板で蓋をします。「ホットサンド」を作る要領で、プレス機で上下から加熱・加圧します。
③ゴム切り&原型取り出し
加熱・加圧したゴムは一つの塊になっているので、メスを使って上下2つに切り開き、中の原型を丁寧に取り出します。するとゴムの内側には「原型+湯道+三角すい」の形の空洞が現れます。これでゴム型の完成。三角すいの注入口からワックスを入れれば、「原型+湯道」の形をしたワックスパターンが作れます。
ようやく下準備が終了。いよいよ実際の製品作りに取り掛かります。
Ⅳ:ワックス・キャスティング
前述の通り、実際の製品製作の流れは、「原型製作」のそれとよく似ています。
①ワックスパターンの作成
溶けたワックスが入った「ワックス・ポット」という機械にゴム型の注入口をセットし、ゴム型内部にワックスを注入します。しばらくするとゴム型内部のワックスが固まるので、中から「ワックスパターン」を取り出します。量産時には必要な個数分、この作業を繰り返します。
②ツリーの製作
土台となるゴム製円すい台の中央に、熱すると溶ける素材でできた棒を一本立てます。その棒に、①で作ったワックスパターンを放射状に溶接し、ツリーを作ります。
③埋没材流し込み
ツリーをステンレス製の筒の中に置き、液状の「埋没材」を流し込みます。
④脱ろう・焼成
この筒を高温の電気炉で焼きます。ツリーは筒内部で溶けて外に流れ出て、空洞になります(=脱ろう)。同時に「埋没材」は硬化します(=焼成)。焼成が終わると、この筒全体が「製品用の型」となります。
⑥キャスティング(=鋳造)
製品に使用したい金属を高温で溶かし、遠心や加圧などの方法で、④の内部にできた空洞に流し込みます。
⑦冷却・埋没材除去
キャスティングが完了した筒を水に入れて冷やします。すると埋没材部分が壊れ、中から地金のツリーが現れます。こびりついた埋没材をきれいに取り除き、ツリーから吹き上がりを切り離します。
作業もいよいよ大詰め。仕上げ作業に入ります。
Ⅴ:仕上げ
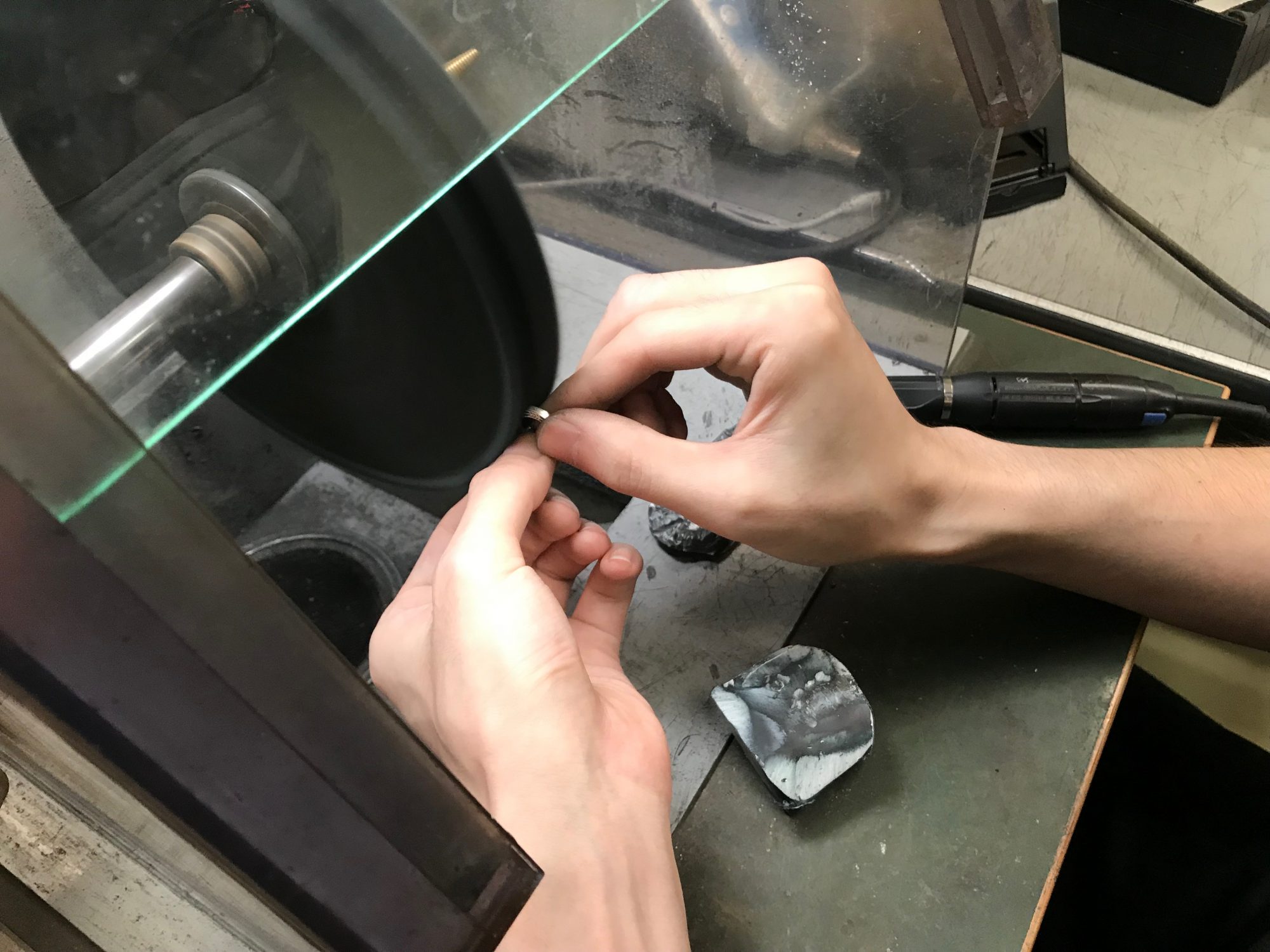
地金部分が完成したので、ここからは仕上げの作業です。何段階にも分けて行う「磨き」はもちろん、刻印、メッキ、いぶし、ロウ付け、石留めなど、デザイン段階で立てた企画に基づき、様々な必要な加工を施していきます。最終的な検品を経て、ようやく製品の完成です!
その華やかな見た目とは裏腹に、ジュエリー製作の工程はとても地道です。しかし素材に使われる貴金属や宝石の美しさは、丁寧な技術があってこそ引き出されるもの。効率優先では、決して生み出すことはできません。
それを下支えするのは、多くのジュエリー職人たちです。妥協せず、自身の最高の技術をもって臨むことが、ジュエリーに対する誠意。「使い手に長く愛してもらえる品になりますように」という職人たちの真っ直ぐな想いが、一つ工程を踏むごとに製品に込められていくのです。
デザイン性や金銭的価値に目が行きがちなジュエリー。しかしあの小さな輝きには、職人たちの心のこもった「温かな価値」が宿っていることも知って頂けると嬉しいです。